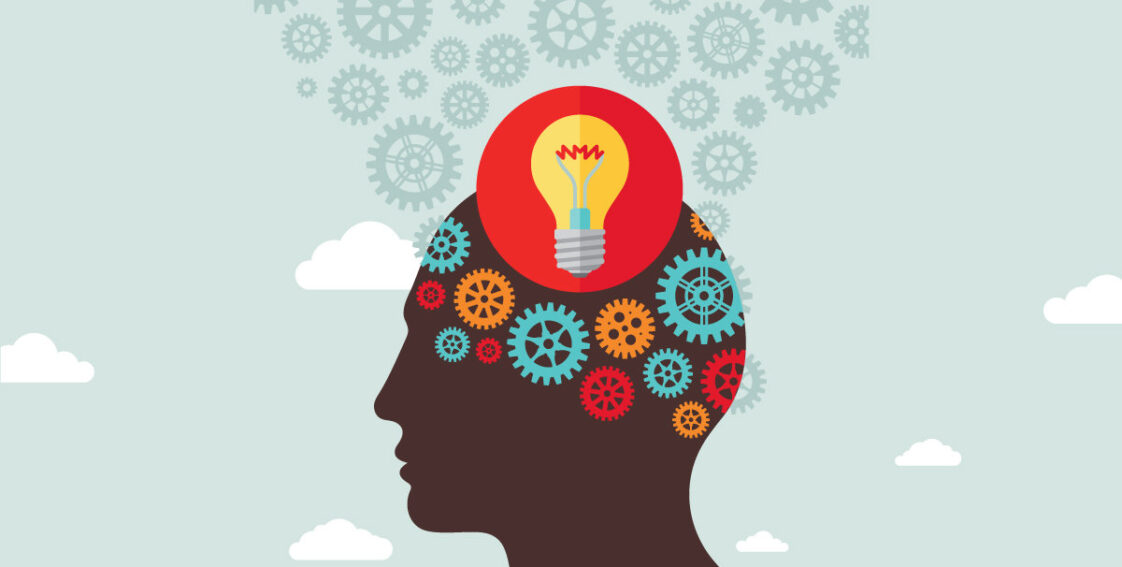
Flex Feeding and Bin Picking have become very popular in recent years. As robot cost and vision capability improve, the technology offers an increasing base of applications.
Flex Feeding provides a minimal part geometry means of getting a part from bulk to an oriented picking condition. The benefits of reduced part geometry dependency and system wear offer for greater flexibility and reconfigurability and lower cost of ownership over time in the automation system.
Bin Picking share much of the same objectives as Flex Feeding; it is another method of getting to a part pick condition from parts in bulk. The direct removal of a part from a container is efficient and can be done for parts which are larger than a Flex Feed system can accommodate and a good alternative to other Floor Feeding and dumping automation scenarios.
The Schneider team has evaluated a few of these products and identified the following as INNOVATION Leaders
INNOVATION AWARD – The SMARTEST Flex Feeder EPSON Robotics IntelliFlex Feeder
The Intelliflex system combines highly advance flex feeding hardware technology and integrated EPSON AI software. The result is easy and automated parameters setup where the feeder and camera run learning sequences to find the best part separation frequency and amplitude settings. Then while running in production the system learns and executes parameter adjustments to improve efficiencies to produce higher pick rates and faster cycle times. There are four sizes of Intelliflex feeder and several lighting, tray and camera options. The Intelliflex feeder integrates seamlessly with the EPSON CV2 vision systems which run on any of EPSON’s robots.
INNOVATION AWARD – Most EFFICIENT Flex Feeder ARS FlexiBowl
ARS FlexiBowl is ideal for small and medium sized parts. Most all Flex feeding systems execute similar functions. They dispense a volume of parts onto an active surface, spread them out to create separation, present them to a vision area and recirculate and/or reorient wrong non-pickable parts. The FlexiBowl’s unique servo driven flat round surface uses a rapid back and forth motion called “shake” which helps spread the parts out and because it’s a rotational surface device the recirculation is naturally occurring. The FlexiBowl is designed in functional quadrants. There is a quadrant for dropping parts from a hopper, a quadrant that bounces the surface to flip parts, a back light quadrant for picking and a quadrant for directional tooling. What’s most unique about the FlexiBowl is that you can be simultaneously dropping and reorienting parts while your picking parts because these functions are occuring in different quadrants. Most all other flex feed systems require you to pause the picking while you are dropping new parts and reorienting. The result of the FlexiBowls simultaneous activities is efficiency and higher pick rates.
INNOVATION AWARD – Most PRACTICAL Bin Pick NEW RCm Bin Pick Automation Cell
Bin Picking is a rapidly developing application area for robots and vision, intended to replace low value added manual content and high cost bulk handling automation. Most system use fairly high technology 3d cameras to look at bulk parts inside of containers then use a robot to pick individual parts from the population. There are significant challenges when doing this. The lighting inside of containers is challenging and needs to factor the shadowing. If its decided to only pick parts that are surface sitting there can be low % or no matches. If its decided to pick parts that are overlapping, Its like playing a game of “Robot Jenga” and there is risk of wear and damage to the robot and gripper from unknown part impingement extraction forces. The RCm bin pick accomplishes the same result but simplifies it by separating the functional elements. Most experienced robot vision tech.s would say, the best way to pick a part with robot and vision is sit the parts on a known Z axis surface and back light them. The RCm bin pick cell has a large 31” square back light with a tempered glass top over a diffuser and is designed with a part sweep to return non- pickable wrong oriented parts to bulk. RCm cell uses custom magnet array technology or vacuum array heads to pull the parts out of impingement and out of bulk and the robot doesn’t enter the container. A lot of the work is in the array design and the application testing. Once parts are on the back lighted surface the same robot using the array can be used to individually pick the parts using another gripper; a second robot can also be used if the rate and circumstances justify it.
To learn more about any of the flex feeding systems above or check out demos please visit our webinars and more page or reach out to a member of our sales team by sending an email to sales@schneider-company.com. We are here to help and will even provide a free two hour parts evaluation if you’re interested!