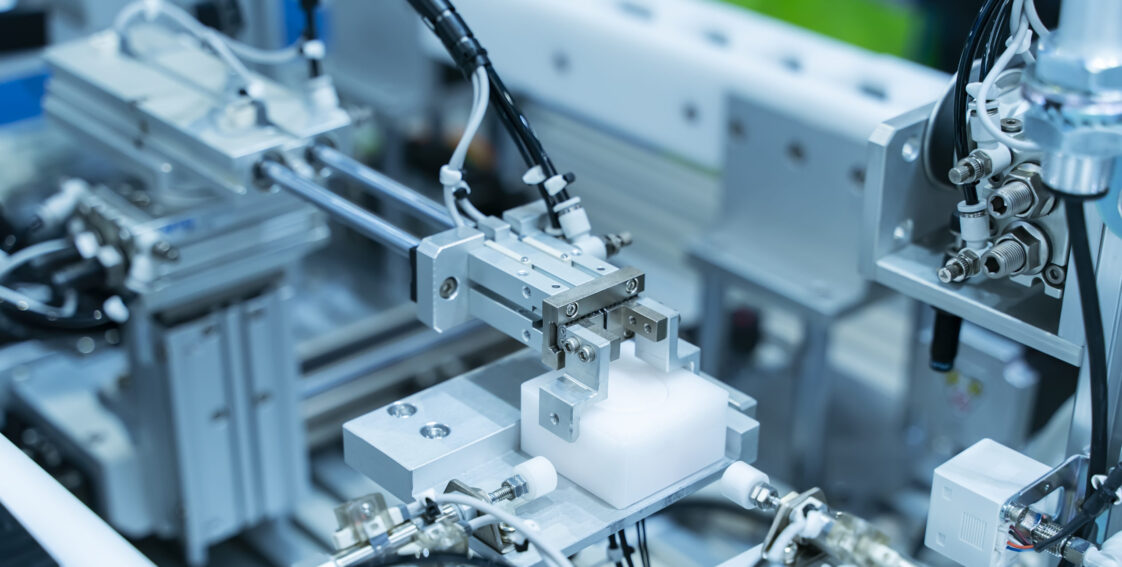
Robotic grippers are used in a variety of industries to move, sort, assemble and package components. There are a surprising range of gripper types and sizes available for your industrial robot arm or automation need. Working with a leading team and a wide product range to help identify the best gripper solution for your industrial automation application is the key to success.
Grippers are just a single category of end of arm tooling solution, or EOAT. Your facility and application determines the best gripper for your material handling or assembly project, but there are some distinct features of different gripper types that you can compare to find the best tooling for your process.
Vacuum Grippers
One of the most common EOAT gripper types is vacuum grippers. These types of robotic grippers also known as vacuum cups alter the atmospheric pressure to create suction, there are often several vacuum cups in a single EOAT design where each carries some of the holding and stabilizing. Most often the vacuum comes from either a centralized vacuum pump or by the use of compressed air and an inline venturi.
Both options offer rapid grip-and-release functionality for your robotic arm. As an EOAT, vacuum grippers are best suited for handling lightweight plastic and fast cycle times or sheet metal components in high-production cycles.
If the components you need to grip and move are irregularly shaped to the extent the vacuum cup bellows can not accomodate the topogrophy or the parts are particularly heavy, this type of EOAT may not be suitable. Vacuum grippers are also not ideal for poor air quality manufacturing environments which can cause clogging and interruptions in the vacuum resulting in the object to fall, for this reason electromechanical vacuum pumps and compressed air venturis require air quality maintenance measures.
They can handle loads that are slightly off-center, but they may not be able to create a vacuum seal on every material and product dimensions. For higher grip strength, consider another style of tooling.
Pneumatic Grippers
This style of gripper looks most like a pair of fingers or a set of jaws. Pneumatic grippers, also known as air -activated mechanical grippers, are a particularly popular EOAT type especially for accurately handling individual parts in a manufacturing process.
The process is to choose the right type and size of gripper and design the finger tool for your particular application. The category of pneumatic grippers is a very diverse one, so you need to size your gripper and tooling design appropriately to provide enough grip force for the weight and speed you desire to move it at. Grippers can be small to pick up electronics components or small medical component or large enough to pick up full-size automotive wheels.
Pneumatic grippers come in two- and three-finger designs which can move parallel or angular. With the right design, you can enjoy high-volume movements with high grip strength. These grippers can be a more specialized and designed for a single specific part or with a large grip range to pick up a greater range of parts. It’s also common for grippers to be attached to tool changers allowing different types of grippers used with the same robot.
A small, two-finger design is capable of picking up precision components without damaging them. Some grippers can grasp items as small as 30 microns with reliable repeatability. Others use larger pneumatic systems to carry large items around your facility with ease.
Choose a two-finger design for simplicity and high-speed use. Three-finger designs can more easily accommodate cylindrical objects where you need to maintaining an accurate center of the part.
Electric Grippers
One of more recent EOAT types, electric grippers are a popular option for collaborative robots. They offer enhanced measuring and sensing capabilities, so your robot arm can recognize the measurements of the components it picks up.
It can also be used around human workers with minimal risk of pinching hands and fingers, thanks to their integral force sensors. Pneumatic grippers operate based on air moving a piston which creates clamping forces. They have limited awareness of an incorrect part being gripped or a humans hand in the way. This makes an electric gripper a safer alternative if employees are working around robot arms which do not have safety guarding or safety scanners to protect them.
You usually have to invest more in electric grippers and they can be comparatively heavy to other options such as pneumatic mechanical and vacuum alternatives.
Explore Robotic Grippers With Schneider and Company
Review the various types of grippers to determine the best option for your robot arm or collaborative robotic assembly. Work with Schneider & Company to identify the right type of gripper or EOAT for your application. Explore the EOAT gripper types today to find the best solution for your industrial manufacturing application.